發布日期:2025-3-27 23:15:17
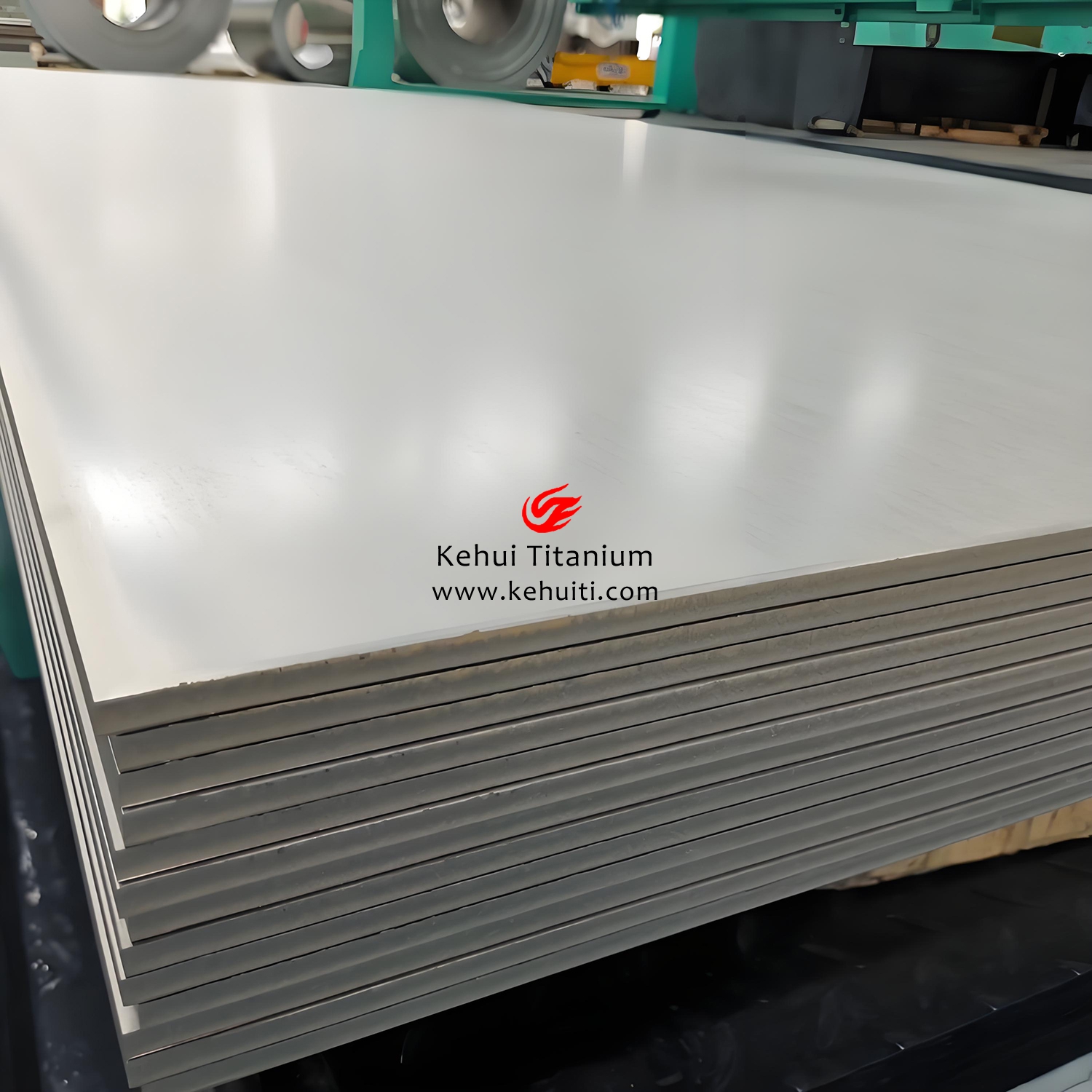
船舶制造用鈦板是以鈦為基加入鋁、錫、鋯等合金元素制成的金屬板材,具有密度低(約為鋼的 1/2)、強度高、耐海水腐蝕性能優異(對海水、氯離子腐蝕抗性遠超不銹鋼,年腐蝕速率<0.001mm)、抗生物附著、低溫韌性好(-196℃仍保持良好力學性能)等特點,材質包括 TA2、TA10、TC4 等工業純鈦及鈦合金。其執行標準涵蓋 GB/T 3621-2020(鈦及鈦合金板材)、GB/T 13810-2021(外科植入物用鈦及鈦合金加工材)(部分船用耐腐蝕部件適用)、ASTM B265(美標鈦板)等。在船舶中主要應用于:①海水管路系統(冷凝管、熱交換器管束),②船體結構(水下殼體、螺旋槳軸系),③甲板設備(索具、緊固件),④LNG 船低溫儲罐內膽等,可大幅降低維護成本、延長船舶服役壽命。隨著綠色船舶、深海船舶需求增長,鈦板在耐蝕、減重、環保(無銅等有害元素滲出)方面的優勢使其前景廣闊。采購時需重點核查耐腐蝕性能檢測報告(如海水腐蝕試驗數據)、板材表面質量(避免劃傷、裂紋)、焊接工藝評定文件,優先選擇通過 DNV GL 等船級社認證的供應商,關注板材厚度公差(通常 ±0.05-0.1mm)及交貨狀態(退火態或熱加工態),并結合船舶設計壓力、溫度等參數選擇適配合金牌號。以下是科輝鈦業關于船舶制造用鈦板的詳細分類說明,以獨立表格形式呈現:
1. 定義
內容 | 描述 |
船舶鈦板定義 | 鈦板是通過軋制或鍛造工藝成形的鈦合金板材,具有卓越耐海水腐蝕、輕量化及抗生物污損特性,專用于船舶殼體、推進系統及海洋平臺等關鍵結構件,顯著延長服役壽命并降低維護成本。 |
2. 材質
牌號 | 成分(wt%) | 適用場景 |
TA1(Gr1) | Ti≥99.6%,Fe≤0.15%,O≤0.10% | 海水管路、熱交換器板片(非承力部件) |
TA10(Ti-0.3Mo-0.8Ni) | Mo 0.2-0.4%,Ni 0.6-0.9% | 高鹽霧環境(如泵閥、螺旋槳軸) |
TC4(Ti-6Al-4V) | Al 5.5-6.8%,V 3.5-4.5% | 深海裝備耐壓殼體(抗外壓≥100 MPa) |
Ti-6Al-4V-Ru(抗縫隙腐蝕) | Ru 0.08-0.14% | 海洋平臺連接法蘭(抗Cl⁻侵蝕) |
3. 性能特點
特性 | 具體表現 |
耐腐蝕性 | 在3.5% NaCl溶液中腐蝕速率<0.001 mm/年,抗氯離子應力腐蝕開裂(SCC)能力優于不銹鋼10倍。 |
抗生物污損 | 微弧氧化表面處理抑制藤壺附著率≥90%。 |
力學性能 | TC4抗拉強度≥895 MPa,延伸率≥10%,深海耐壓性能(等效1000米水深)。 |
輕量化 | 密度(4.5 g/cm³)僅為鋼的57%,相同強度下減重40%。 |
4. 執行標準
標準類型 | 標準號 | 適用范圍 |
中國國標 | GB/T 3621-2007 | 鈦及鈦合金板材通用標準 |
國際標準 | ASTM B265-20 | 鈦及鈦合金板材規范 |
船舶標準 | DNVGL-OS-C401 | 海洋工程鈦材設計與制造要求 |
行業規范 | ISO 21457:2022 | 海洋設備材料耐蝕性評估 |
5. 加工工藝
工藝步驟 | 關鍵參數 |
熱軋 | β相區軋制(TC4:950-1000℃),變形量≥70%,晶粒度≤ASTM 6級。 |
冷軋 | 室溫軋制變形量≤30%,中間退火(700℃×1h)消除加工硬化。 |
焊接 | 激光-氬弧復合焊(保護氣體:氬氣+5%氦氣),焊縫強度系數≥95%。 |
表面處理 | 微弧氧化(電壓400-600V)生成20-50μm陶瓷層,抗微生物附著。 |
6. 關鍵技術
技術領域 | 突破點 |
大尺寸軋制 | 寬幅(≥2.5m)鈦板軋制技術,厚度公差±0.1mm。 |
深海焊接 | 高壓干法焊接(水深≥3000米,真空度≤1×10⁻³ Pa)。 |
抗污損設計 | 仿生鯊魚皮表面微結構(流體阻力降低15%)。 |
7. 加工流程
步驟 | 流程說明 |
1. 熔煉提純 | 真空自耗電弧爐(VAR)熔煉成低雜質鈦錠(O≤0.15%)。 |
2. 熱軋開坯 | β相區軋制至中厚板(厚度10-30mm)。 |
3. 冷軋精整 | 多道次冷軋至目標厚度(2-20mm),中間退火。 |
4. 表面處理 | 酸洗(HF+HNO₃)或微弧氧化。 |
5. 檢測驗收 | 超聲探傷(ASME V標準)+ 鹽霧試驗(5000小時)。 |
8. 具體應用領域
應用部件 | 功能需求 |
船體結構板 | 抗海水腐蝕,替代涂層鋼(壽命延長3倍)。 |
船舶螺旋槳 | 抗空泡腐蝕(疲勞壽命≥10⁸次循環)。 |
海水淡化蒸發器 | 耐高溫濃鹽水(Cl⁻濃度≥60,000 ppm)。 |
海洋平臺樁腿 | 抗洋流沖刷及陰極保護兼容性。 |
9. 與其他船舶材料對比
材料類型 | 鈦板優勢 | 鈦板劣勢 |
雙相不銹鋼(2205) | 耐點蝕能力提升5倍,免維護 | 初始成本高3-4倍 |
銅鎳合金(B10) | 無電偶腐蝕風險,壽命延長2倍 | 強度低25%-30% |
玻璃鋼(GFRP) | 可焊接修復,抗沖擊性更優 | 耐溫上限低(≤80℃) |
10. 未來發展新領域
方向 | 具體內容 |
綠色船舶 | 鈦板制造氫燃料電池雙極板(接觸電阻≤5 mΩ·cm²)。 |
深海采礦 | 耐磨損鈦合金(TiB2增強)用于礦石輸送管道。 |
3D打印技術 | 激光選區熔化(SLM)制造復雜流道鈦板(孔隙率50-70%)。 |
11. 技術挑戰與前沿攻關
挑戰領域 | 攻關方向 |
成本控制 | 短流程熔軋一體化技術(加工能耗降低30%)。 |
極端環境適應 | 開發抗氫脆鈦合金(添加稀土元素釔)。 |
智能監測 | 嵌入式光纖傳感器實時監測腐蝕與應力狀態。 |
12. 趨勢展望
趨勢 | 預測內容 |
深海裝備普及 | 鈦板在3000米以上深海工程滲透率提升至40%(2030年)。 |
智能化制造 | 數字孿生技術優化軋制參數(良率提升至99.5%)。 |
循環經濟 | 廢鈦板回收率從60%提升至90%(電解精煉技術)。 |
以上表格基于船舶與海洋工程領域最新標準(如DNVGL-OS-C401)及2023年國際海洋技術會議成果整理,涵蓋鈦板在船舶制造中的核心特性、工藝難點及未來發展方向,適用于船體設計、海洋裝備選型及制造工藝優化參考。
tag標簽:船舶制造用鈦板